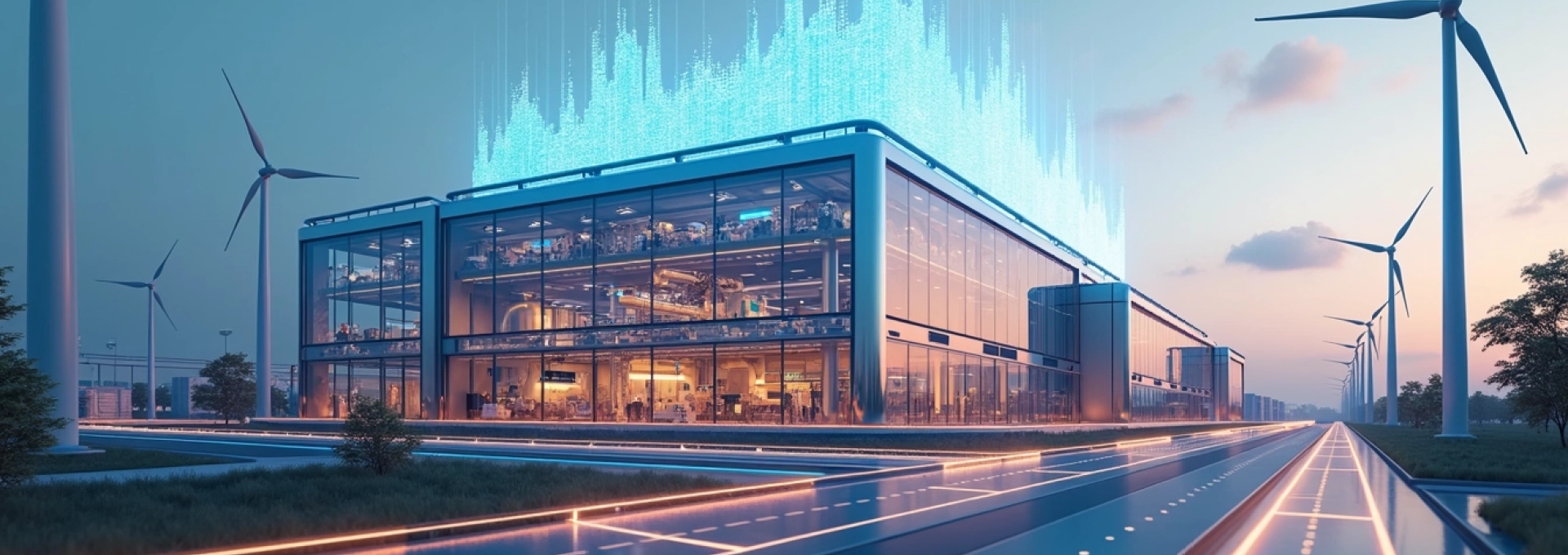
La réduction de la consommation énergétique est devenue un enjeu majeur pour le secteur industriel. Face à la hausse des coûts de l'énergie et aux préoccupations environnementales croissantes, les entreprises cherchent des solutions innovantes pour optimiser leur efficacité énergétique. Cette démarche permet non seulement de réaliser des économies substantielles, mais aussi de réduire l'empreinte carbone et d'améliorer la compétitivité. Quelles sont les stratégies les plus efficaces pour diminuer la consommation d'énergie dans l'industrie ?
Audit énergétique industriel : méthodologies et normes ISO 50001
L'audit énergétique constitue la pierre angulaire de toute démarche d'optimisation énergétique industrielle. Il permet d'établir un diagnostic précis de la consommation d'énergie d'une entreprise et d'identifier les gisements d'économies potentiels. La norme ISO 50001, référence internationale en matière de management de l'énergie, fournit un cadre méthodologique rigoureux pour mener à bien cet audit.
La première étape consiste à collecter et analyser les données de consommation énergétique de l'ensemble des équipements et process industriels. Des outils de mesure sophistiqués sont déployés pour obtenir une cartographie détaillée des flux énergétiques. L'analyse de ces données permet d'identifier les postes les plus énergivores et de détecter d'éventuelles anomalies ou gaspillages.
Ensuite, les auditeurs procèdent à une inspection approfondie des installations, examinant l'état des équipements, leur niveau d'isolation, leur régulation, etc. Ils étudient également l'organisation du travail et les pratiques des opérateurs pour repérer d'éventuelles sources d'inefficacité énergétique.
Sur la base de ce diagnostic, des recommandations d'amélioration sont formulées, assorties d'une estimation des investissements nécessaires et des économies potentielles. Ces préconisations peuvent aller du simple réglage d'équipements à des projets plus conséquents comme le remplacement de lignes de production énergivores.
La norme ISO 50001 va plus loin en proposant un système de management de l'énergie complet. Elle encourage les entreprises à mettre en place une politique énergétique structurée, avec des objectifs chiffrés et un suivi régulier des performances. Cette approche systémique permet d'inscrire l'optimisation énergétique dans une démarche d'amélioration continue.
Technologies d'efficacité énergétique pour l'industrie
L'innovation technologique offre un large éventail de solutions pour réduire la consommation énergétique industrielle. Ces technologies, en constante évolution, permettent d'optimiser les process existants et d'explorer de nouvelles approches plus économes en énergie.
Systèmes de récupération de chaleur fatale
La chaleur fatale, ou chaleur perdue, représente un gisement d'économies considérable dans l'industrie. Des technologies innovantes permettent désormais de capter et de valoriser cette énergie thermique qui serait autrement gaspillée. Les échangeurs de chaleur nouvelle génération, par exemple, offrent des rendements exceptionnels pour récupérer la chaleur des fumées, des eaux usées ou des process industriels.
Ces systèmes peuvent être couplés à des pompes à chaleur industrielles pour augmenter la température de la chaleur récupérée et la réinjecter dans les process ou l'utiliser pour le chauffage des locaux. Certaines industries parviennent ainsi à réduire leur consommation énergétique de 30% grâce à ces technologies.
Moteurs électriques à haut rendement et variateurs de vitesse
Les moteurs électriques sont omniprésents dans l'industrie et représentent une part importante de la consommation électrique. L'adoption de moteurs à haut rendement de classe IE3 ou IE4 permet de réaliser des économies significatives. Ces moteurs offrent des performances supérieures grâce à une conception optimisée et l'utilisation de matériaux plus performants.
Associés à des variateurs de vitesse électroniques, ces moteurs voient leur efficacité encore améliorée. Les variateurs permettent d'adapter précisément la vitesse du moteur aux besoins réels du process, évitant ainsi les gaspillages liés au fonctionnement à vitesse constante. Dans certaines applications, les économies d'énergie peuvent atteindre 50%.
Éclairage LED et systèmes de gestion intelligente
Bien que l'éclairage ne représente généralement qu'une part modeste de la consommation énergétique industrielle, son optimisation offre un retour sur investissement rapide. Le passage à l'éclairage LED permet de réduire la consommation de 50 à 80% par rapport aux technologies traditionnelles.
L'intégration de systèmes de gestion intelligente de l'éclairage amplifie ces économies. Des capteurs de présence et de luminosité permettent d'adapter l'éclairage aux besoins réels, tandis que des systèmes centralisés optimisent la consommation à l'échelle d'un site industriel entier.
Optimisation des process de combustion industrielle
Les process de combustion, omniprésents dans l'industrie, offrent un potentiel d'optimisation considérable. Les technologies de combustion à oxygène pur permettent d'améliorer significativement le rendement énergétique des fours industriels. En remplaçant l'air par de l'oxygène pur, on élimine l'azote inutile et on obtient des températures plus élevées avec moins de combustible.
Les brûleurs à faibles émissions de NOx constituent une autre avancée majeure. Ils permettent de réduire la consommation de combustible tout en limitant les émissions polluantes. Couplés à des systèmes de régulation avancés, ces brûleurs peuvent générer des économies d'énergie de l'ordre de 15 à 20%.
Digitalisation et industry 4.0 pour l'optimisation énergétique
La révolution numérique offre de nouvelles perspectives pour l'optimisation énergétique industrielle. Les technologies de l'Industrie 4.0 permettent une gestion plus fine et réactive de la consommation d'énergie, ouvrant la voie à des gains d'efficacité considérables.
Iot et capteurs pour le monitoring énergétique en temps réel
L'Internet des Objets (IoT) révolutionne le monitoring énergétique industriel. Des capteurs connectés, disséminés dans l'ensemble des installations, collectent en continu des données sur la consommation d'énergie, les températures, les pressions, etc. Ces informations sont centralisées et analysées en temps réel, offrant une vision globale et détaillée de la performance énergétique de l'usine.
Cette approche permet de détecter instantanément les anomalies ou les dérives de consommation. Par exemple, une augmentation soudaine de la consommation électrique d'un moteur peut signaler un problème mécanique naissant. Le monitoring en temps réel permet ainsi d'agir de manière préventive, évitant les gaspillages énergétiques et les pannes coûteuses.
Intelligence artificielle et machine learning pour la prédiction de consommation
L'intelligence artificielle (IA) et le machine learning apportent une dimension prédictive à la gestion énergétique industrielle. En analysant les données historiques de consommation couplées à de multiples variables (production, météo, etc.), ces algorithmes peuvent prédire avec précision les besoins énergétiques futurs.
Cette capacité prédictive permet d'optimiser la production et le stockage d'énergie, particulièrement pertinent dans le contexte d'une intégration croissante des énergies renouvelables. L'IA peut également suggérer des ajustements en temps réel des paramètres de production pour minimiser la consommation énergétique tout en maintenant la qualité des produits.
Jumeaux numériques pour la simulation et l'optimisation des process
Le concept de jumeau numérique gagne du terrain dans l'industrie. Il s'agit d'une réplique virtuelle d'un équipement ou d'un process industriel, intégrant l'ensemble des données physiques et de fonctionnement. Cette représentation numérique permet de simuler et d'optimiser les process sans perturber la production réelle.
En matière d'optimisation énergétique, les jumeaux numériques offrent des possibilités fascinantes. Ils permettent de tester virtuellement différents scénarios d'amélioration, d'identifier les configurations optimales et de prédire l'impact des changements avant leur mise en œuvre. Cette approche réduit considérablement les risques et les coûts liés à l'optimisation des process industriels.
Transition vers les énergies renouvelables dans l'industrie
La transition vers les énergies renouvelables représente un levier majeur pour réduire l'empreinte carbone de l'industrie et sécuriser son approvisionnement énergétique à long terme. De nombreuses technologies matures permettent aujourd'hui d'intégrer efficacement les énergies vertes dans les process industriels.
Intégration de panneaux solaires photovoltaïques sur sites industriels
L'énergie solaire photovoltaïque connaît un essor remarquable dans le secteur industriel. Les vastes surfaces de toitures des usines et entrepôts offrent un potentiel considérable pour l'installation de panneaux solaires. Les progrès technologiques ont permis d'améliorer significativement le rendement et la durabilité des panneaux, rendant l'investissement de plus en plus attractif.
L'autoconsommation solaire permet aux industriels de réduire leur dépendance au réseau électrique et de maîtriser leurs coûts énergétiques sur le long terme. Dans certains cas, la production solaire peut même être couplée à des systèmes de stockage par batteries pour optimiser l'utilisation de l'énergie produite.
Cogénération et trigénération à partir de biomasse
La cogénération, qui consiste à produire simultanément de l'électricité et de la chaleur, offre des rendements énergétiques très élevés. Lorsqu'elle est alimentée par de la biomasse (déchets de bois, résidus agricoles, etc.), elle permet de valoriser des ressources locales et renouvelables.
La trigénération va encore plus loin en ajoutant la production de froid, particulièrement intéressante pour certaines industries agroalimentaires ou chimiques. Ces systèmes peuvent atteindre des rendements globaux supérieurs à 80%, offrant une solution très efficace pour réduire la consommation d'énergie fossile.
Géothermie industrielle : applications et potentiel
La géothermie, longtemps sous-exploitée dans l'industrie, connaît un regain d'intérêt. Elle offre une source d'énergie stable et prévisible, particulièrement adaptée aux besoins de chaleur constants de nombreux process industriels. Les techniques de forage modernes permettent d'accéder à des ressources géothermiques de plus en plus profondes et chaudes.
Les applications industrielles de la géothermie sont multiples : chauffage de serres, séchage de produits agricoles, préchauffage de process, etc. Dans certains cas, la géothermie haute température peut même être utilisée pour produire de l'électricité, offrant une solution d'approvisionnement énergétique complète et durable.
Stratégies managériales et organisationnelles pour la réduction énergétique
Au-delà des solutions technologiques, l'optimisation énergétique industrielle repose en grande partie sur des approches managériales et organisationnelles. L'implication de l'ensemble des collaborateurs et la mise en place de processus structurés sont essentielles pour pérenniser les gains d'efficacité énergétique.
Formation et sensibilisation des équipes aux enjeux énergétiques
La sensibilisation et la formation des équipes sont cruciales pour ancrer la culture de l'efficacité énergétique dans l'entreprise. Des programmes de formation adaptés permettent aux opérateurs de comprendre l'impact de leurs actions sur la consommation d'énergie et d'adopter les bonnes pratiques au quotidien.
Ces formations peuvent couvrir des aspects techniques (utilisation optimale des équipements, détection des anomalies) mais aussi des notions plus générales sur les enjeux énergétiques et environnementaux. L'objectif est de faire de chaque employé un acteur de l'optimisation énergétique.
Mise en place d'un système de management de l'énergie (SME)
Un Système de Management de l'Énergie (SME) fournit un cadre structuré pour intégrer l'efficacité énergétique dans tous les aspects de l'entreprise. Basé sur le principe de l'amélioration continue, le SME implique la définition d'objectifs énergétiques, la mise en place de plans d'action et un suivi régulier des performances.
La norme ISO 50001 offre un référentiel reconnu pour mettre en place un SME efficace. Elle guide les entreprises dans l'élaboration d'une politique énergétique cohérente et la mise en œuvre de processus d'optimisation systématiques. Un SME bien conçu peut conduire à des réductions de consommation énergétique de l'ordre de 10 à 20% dans les premières années de mise en œuvre.
Lean manufacturing et kaizen pour l'optimisation des flux énergétiques
Les principes du lean manufacturing et
du kaizen (amélioration continue) peuvent être appliqués avec succès à l'optimisation énergétique. Ces approches, issues du monde industriel japonais, visent à éliminer systématiquement les gaspillages et à optimiser les flux, y compris les flux énergétiques.
L'application du lean à l'énergie implique une analyse détaillée de la chaîne de valeur énergétique, de la production à la consommation finale. On cherche à identifier et éliminer toutes les étapes qui ne créent pas de valeur. Par exemple, le chauffage ou l'éclairage de zones inoccupées, le fonctionnement d'équipements à vide, etc.
Le kaizen encourage la mise en place de petites améliorations continues plutôt que de grands changements brutaux. Cette approche peut être particulièrement efficace pour l'optimisation énergétique, en impliquant les opérateurs dans l'identification et la mise en œuvre de solutions d'économie d'énergie au quotidien.
Financement et incitations pour les projets d'efficacité énergétique
La mise en œuvre de projets d'efficacité énergétique peut nécessiter des investissements conséquents. Heureusement, il existe de nombreux mécanismes de financement et d'incitation pour aider les industriels à franchir le pas.
Certificats d'économies d'énergie (CEE) pour l'industrie
Le dispositif des Certificats d'Économies d'Énergie (CEE) est un levier puissant pour financer les projets d'efficacité énergétique dans l'industrie. Ce mécanisme oblige les fournisseurs d'énergie à promouvoir l'efficacité énergétique auprès de leurs clients, sous peine de pénalités financières.
Pour l'industrie, cela se traduit par des aides financières significatives pour la mise en œuvre d'actions standardisées d'économies d'énergie. Ces actions couvrent un large spectre, de l'isolation des bâtiments à l'optimisation des process industriels. Le montant de l'aide dépend du volume d'économies d'énergie généré par l'action.
Les CEE peuvent ainsi financer une part importante des investissements en efficacité énergétique, réduisant considérablement le temps de retour sur investissement des projets.
Programmes ADEME et aides régionales à la transition énergétique
L'Agence de l'Environnement et de la Maîtrise de l'Énergie (ADEME) propose de nombreux programmes d'aide aux entreprises pour leurs projets d'efficacité énergétique. Ces aides peuvent prendre la forme de subventions, d'avances remboursables ou de prêts à taux bonifiés.
Par exemple, le Fonds Chaleur de l'ADEME soutient le développement de la production de chaleur renouvelable dans l'industrie (biomasse, géothermie, solaire thermique). L'ADEME propose également des aides pour la réalisation d'études de faisabilité ou d'audits énergétiques.
En complément, les régions proposent souvent leurs propres dispositifs d'aide à la transition énergétique des entreprises. Ces aides peuvent être cumulées avec les dispositifs nationaux, offrant ainsi un effet de levier important pour le financement des projets.
Contrats de performance énergétique (CPE) avec les ESCO
Les Contrats de Performance Énergétique (CPE) offrent une solution innovante pour financer et mettre en œuvre des projets d'efficacité énergétique. Dans ce modèle, une entreprise de services énergétiques (ESCO) prend en charge l'investissement et la mise en œuvre des actions d'économies d'énergie. Elle se rémunère ensuite sur les économies réalisées.